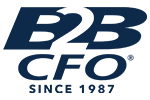
Implementing Fishbowl Inventory In A Manufacturing Business
Posted on March 15, 2020 by Rick Daigle
In November 2009 I was hired to select and implement a business application in a Paint Manufacturing business. For the prior 15 years the company had used QuickBooks but had never gotten the training or consulting help to set up their inventory items correctly. They had tracked their COGS via countless spreadsheets and did manual Inventory Adjustments and Journal Entries each month to get to their COGS and Inventory Asset values. As you can imagine the accuracy of their financials was very suspect.
This company had enjoyed $3M to $4M in revenue the past few years with most of the sales coming from craft paints. They have a new product line called RESTORE which is a deck, dock, and concrete resurfacing paint which is fantastic. Two coats of this paint and your back deck or boat dock has lifetime protection from the elements. They expect to do $6M in 2010 on this product alone.
The owner and I shared a mutual friend who is an investment banker. The IB was discussing possible funding for the growth but was concerned about the accuracy of the financials as the company started this important phase. I was called in to determine if they could use the latest version of QB Enterprise to run their manufacturing operations, track inventory, and capture costs accurately through the manufacturing process.
At a high level they mix large batches of intermediate paint, then mix those with colorants and other chemicals in separate batches, and finally package the paint in 2oz, 8oz, 12oz, or gallon size products. The challenge was to get the final COGS of any individual product to include the costs of raw materials, paint, bottles, caps, boxes, shrink wrap, etc. Every cost along the manufacturing process had to be included in the finished good.
It didn’t take long to realize that QB was not going to handle this. So I then began a search process to find an application which would meet the demands of a SMB manufacturing operations. I identified FishBowl Inventory as a likely candidate and executed the evaluation and determined that it would indeed fit our needs.
During the month of December we extracted data from legacy applications to create Import files for:
- 6,000 Parts (raw materials, packaging, etc.)
- 1,000 Finished Products
- 4,000 Bill of Materials (Paint recipes and Finished Goods)
- 800 Customers
- 200 Vendors
We spent a month testing, training, and preparing for physical inventory and go-live on January 3, 2010.
We were very successful with this implementation. In the 5 weeks we have been running the business on Fishbowl Inventory we have completed over 500 work orders. There are 3 deliverables which are invaluable to this company:
- They now know the exact cost of every single bottle/can of paint they package to 5 decimal places.
- They know exactly which raw materials to purchase and when to purchase.
- They know exactly which finished products to make and when to make them based on sales data.
Look for the RESTORE product in your area this spring/summer at the nearest Home Depot, Lowe’s, or ACE Hardware stores.
And, if you are looking for a Fishbowl Inventory expert . . . . call Rick Daigle, 404-787-5835, or email to rdaigle@b2bcfo.com.
